Observation and Measurement of Rubber Using a Digital Microscope
Rubber is an elastic polymer compound used in various industries, including for tyres, hoses, and belts. This section introduces observation and measurement examples of rubber using a digital microscope.
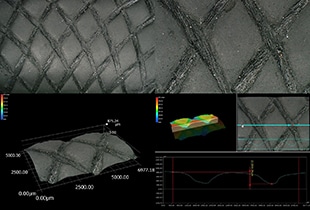
- Differences between natural and synthetic rubbers
- Characteristics of natural and synthetic rubbers
- Types, characteristics, and applications of typical synthetic rubber
- Shape-based categories of rubber
- Hardness of rubber
- Observation and measurement examples of rubber using a digital microscope
Differences between natural and synthetic rubbers
- Natural rubber
-
Rubber products made through vulcanisation* of raw rubber—dried rubber tree sap (latex)—are categorised as natural rubber (NR).
- * Vulcanisation:
- Sulphur is added to raw rubber and heated to bring about intermolecular bonding, which improves the elasticity and strength of the rubber. Since being accidentally discovered in 1839 by Charles Goodyear of the United States, rubber has become an industrialised material.
- Synthetic rubber
- “Synthetic rubber” is a generic term for rubber that has been chemically synthesised from petroleum. There are more than 100 types of synthetic rubber made from various raw materials. Developed during World War II, synthetic rubber is a relatively new product. Because natural rubber, mainly produced in Southeast Asia, was difficult to obtain in the United States and Germany, both countries began producing synthetic rubber domestically. Since then, use has become widespread.
Characteristics of natural and synthetic rubbers
Natural rubber accounts for about 40% of global use, and synthetic rubber accounts for the remaining 60%. Each is used accordingly depending on the application.
Natural rubber
- Advantages
- The high elasticity and tear strength of natural rubber make it a common choice for large tyres for trucks and buses, and various other industrial applications.
- Disadvantages
- Natural rubber has a low resistance to weather, heat, and oil, so it is vulnerable to light, heat, rain, and other environments.
Synthetic rubber
- Advantages
- Compared with natural rubber, synthetic rubber has fewer impurities and offers greater performance stability. Changing the composition of the raw materials makes it possible to produce rubber with a variety of properties, including high resistance to heat, chemicals, or abrasion.
- Disadvantages
- Synthetic rubber has inferior elasticity and tear strength than natural rubber.
Types, characteristics, and applications of typical synthetic rubber
Synthetic rubber can be generally categorised as either general-purpose rubber or specialty rubber. The typical names, characteristics, and applications are as follows.
General-purpose rubber
- Isoprene rubber (IR)
-
With almost the same properties as natural rubber, isoprene rubber has good colour and low odour, and doesn’t require any heat retention even at low temperatures. However, natural rubber offers better weather and heat resistance.
- Applications:
- Commonly used for automobile and aircraft tyres, conveyor belts, and table tennis rackets with colour added.
- Styrene-butadiene rubber (SBR)
-
Styrene-butadiene rubber is the most widely produced general-purpose rubber and offers better abrasion and ageing resistance than natural rubber. Due to its poor oil resistance, however, it is not suitable for O-rings and gaskets.
- Applications:
- Commonly used for automobile tyres, shoe soles, and floor tiles.
- Butadiene rubber (BR)
-
Butadiene rubber is the second most widely produced type of rubber after styrene-butadiene rubber. It offers better elasticity and abrasion resistance than natural rubber. Due to its poor oil resistance, however, it is not suitable for O-rings and gaskets.
- Applications:
- Commonly used for automobile tyres, rubber belts, and hoses. It is also the main raw material for ABS (acrylonitrile butadiene styrene) plastic.
Specialty rubber
- Nitrile rubber (NBR)
-
Nitrile rubber is highly resistant to oil, abrasion, and ageing, and is widely used for oil-resistant rubber.
- Applications:
- Commonly used for O-rings, packing, gaskets, and seals.
- Chloroprene rubber (CR)
-
Chloroprene rubber offers excellent resistance to heat, weather, ozone, and flames.
- Applications:
- Commonly used as a coating material for automobile belts, hoses, wires, and cables, and is also used in adhesives and paints due to its high adhesion performance.
- Butyl rubber (IIR)
-
Butyl rubber offers high heat, vibration, and chemical resistance in addition to excellent electrical insulation properties.
- Applications:
- Commonly used for tyre inner tubes due to the low gas permeability of the rubber, as soundproofing material for audio equipment, and as coating material for electric wires.
- Ethylene-propylene rubber (EPM/EPDM)
-
Ethylene-propylene rubber offers high resistance to ageing, weather, ozone, and deterioration when used outdoors. However, resistance to oil is very low.
- Applications:
- Commonly used for automotive parts (radiator hoses, belts, etc.), coating for electric wires, and construction materials.
- Acrylic rubber (ACM)
-
In addition to excellent heat, weather, and ozone resistance, acrylic rubber also offers high oil resistance at high temperatures. Resistance to cold and chemicals, however, is low.
- Applications:
- Commonly used for automobile oil hoses, gaskets, and seals.
- Silicone rubber (Q)
-
Despite its low tensile and mechanical strength, silicone rubber offers extremely high resistance to cold and heat, weather, and ozone in addition to high electrical insulation properties.
- Applications:
- Commonly used for food packaging/containers and medical products due to it being harmless to the body and highly resistant to heat.
- Fluororubber (FKM)
-
Fluororubber is extremely resistant to heat and chemicals, but costs a lot.
- Applications:
- Commonly used for food and pharmaceutical equipment and equipment components.
- Urethane rubber (U)
-
Urethane rubber offers excellent tensile strength and load-bearing performance as well as high oil and abrasion resistance. However, heat and water resistance are low.
- Applications:
- Commonly used for components that support heavy objects, including for tyres, shoe soles, and rollers.
Shape-based categories of rubber
- Sheets
- Rubber can be processed into sheets.
This shape is then used for processing into gaskets, packing, and seals. - Foam
- Rubber can be blended with a foaming agent for processing into a porous structure (sponge).
There are two main types of foams.


Hardness of rubber
A hardness scale of 0 to 100 is used to indicate the hardness of rubber, with 0 being the softest and 100 being the hardest.

- a: Marshmallow
- b. Gummy candy
- c: Tyre
- d: Baseball
- e: Golf ball
Observation and measurement examples of rubber using a digital microscope
The latest examples of observation and measurement of rubber using KEYENCE’s VHX Series 4K Digital Microscope are introduced below.


Optical Shadow Effect Mode image
Optical Shadow Effect Mode can be used to visualise minute irregularities on the surface of black rubber.




3D image
Using 3D imaging makes it possible to visualise irregularities on the surface of the white rubber.


Optical Shadow Effect Mode colour map image
Colour map images make it possible to visualise belt wear conditions.


ZS-20, 30×, automatic area measurement image
The automatic area measurement function makes it possible to quantify the deterioration of rubber.


Automatic area measurement image
The automatic area measurement function makes it possible to quantify rubber particles.

ZS-200, 200×, ring illumination + HDR
The HDR function allows for detailed observation of cross-sections of foam rubber.